优化印刷工艺(收集5篇)
来源:
优化印刷工艺篇1
无水胶印,简单的说,就是没有“水”参与的胶版印刷工艺,特殊的无水胶印印版和对滚筒表面温度的精准控制,是实现无水胶印的两个重要因素。相比传统的有水胶印,由于剔除了水的影响,从根本上解决了相应的质量问题,无水胶印拥有更完美的印刷效果。分析这张有水胶印和无水胶印的印版对比简图,我们就可以轻而易举的发现无水胶印印版在油墨传递方面的优势所在。
同时,无水胶印工艺还具有以下的优点:
?没有水墨平衡问题,最少的废品,更少的纸张消耗量;
?更好、更稳定的印刷质量(网点还原效果好、细部清晰、颜色鲜艳);
?没有扇形变形和纸带张力问题,使得套印更精准;
?没有润版装置和润版液添加剂,提高了环保性能;
目前,无水胶印印版的耐印力已达到12万到15万(滚筒)转,在理想条件下可超过20万转,其价格也随着市场需求量的不断扩大而逐渐降至更合理的范围,如果考虑到其完美印刷质量所带来的更大盈利空间,低废品率所节省的日常生产纸张成本,以及没有润版液消耗成本等因素,版材价格根本不会成为限制无水胶印应用的因素。
然而,当今市场上采用无水工艺的印刷机并不多见,其主要原因是很多印刷机制造厂商至今不能完美解决的一个技术问题――对滚筒和墨辊的表面温度的高效控制。
作为拥有近200年历史的全球最具规模的胶印机制造企业之一的高宝公司,早已在多年前便凭借着自身在胶印机制造领域的丰富经验和不断创新的精神,突破了这一技术瓶颈,推出了真正适用于大印量、满负荷日常生产的(以报纸印刷为例:额定产量为9万份/时)轮转无水胶印机――KBACortina。我们可以通过示意图了解Cortina实现无水印刷的基本设计理念。
一个配备有Newsflow供墨装置和PlateTronic自动换版装置的Cortina印刷色组:
1.橡皮布滚筒
2.印版滚筒(可进行温度控制的)
3.自动换版装置(选购)
4.靠版墨辊(有橡胶涂覆层)
5.串墨辊(有耐纶涂覆层)
6.匀墨辊(有橡胶涂覆层)
7.网纹辊(陶瓷的、可进行温度控制的)
8.刮墨刀
9.供墨管
10.配备有集成墨泵的墨斗
11.橡皮布清洗装置
Cortina的Newsflow无墨键供墨装置是专门为进行高速无水卷筒纸胶印而设计制造的。油墨经由刮墨刀、网纹辊和两根靠版墨辊被连续泵送到印版上,与油墨覆盖率无关。两根串墨辊和两根附加的匀墨辊确保形成完美平滑的墨膜。乳化――这个在传统胶印中非常常见的问题在Cortina上根本不会发生。
保存在印刷机软件中的电子温度控制曲线根据印刷机速度自动调节网纹辊和印版滚筒的表面温度。无论印刷机速度如何,都可保证施涂均匀的无糊版问题的油墨(如Ifra标准要求的全实地密度)。在以秒为单位的数秒时间内,迅速将印版滚筒和供墨网纹辊的表面温度调整至所需数值,这一专利技术,正是Cortina印刷机能够满足大规模工业化印刷生产的核心技术之一。除此之外,其颠覆传统的左右分离式紧凑型结构设计,在印刷过程中缩短了纸路长度,也是Cortina呈现完美印刷质量的关键。
优化印刷工艺篇2
关键词:印刷技术发展现状发展趋势
随着社会经济的不断发展,大力发展节约型产业、实现经济结构转型成为当前经济发展的新任务,党的十八届五中全会确立的创新、协调、绿色、开放、共享“五大发展理念为包装行业发展提供了发展思路,同时基于“互联网+”行动的实施印刷由过去的粗狂型发展模式转化为个性化、精品化的方向。但与发达国家相比,我国印刷业的总产值仍然很低。基于社会对印刷行业的新要求,要求印刷技术要不断进行技术创新,以此适应社会发展的需求。
1印刷的概述
印刷(Printing,GraphicArts,GraphicCommunications)是把文字、图画、照片等原稿经制版、施墨、加压等工序,使油墨转移到纸张、织品、皮革等材料表面上,批量复制原稿内容的技术。简单意义上说,印刷是使用印版或其他方式将原稿上的图文信息转移到承印物上的工艺技术,也可以理解为使用模拟或数字的图像载体将呈色剂/色料(如油墨)转移到承印物上的复制过程。
印刷技术在我国具有悠久的历史,其代表着中华民族的优秀文化,是人类智慧的结晶,现存最早文献和最早的中国雕版印刷实物是在公元600年,即唐朝初期。随着经济的发展,印刷技术在生产实践中的应用比较广泛,可以说各行各业都离不开印刷,总体来看印刷技术主要包括:平版印刷、凸版印刷(含柔版工艺)、凹版印刷、丝网印刷和数字印刷并存的结局。一般来说胶印工艺在我国印刷历史中的时间比较长,而且其因制作成本低廉,而受到实践的广泛应用,但是其具有高耗能的缺点,不利于我国当前大力发展节约型资源的经济发展要求。柔性印刷则兼具了许多印刷工艺的优点,柔性印刷在印刷的时候具有印刷压力小,印迹清晰的特点,尤其是印刷对象的广泛性,其不仅能够适应高质量的纸板,而且还适应于质量低劣的纸板,但是其版材比较贵,因此制造成本相对比较高,尤其是不适合小批量的生产;凹印工艺具有很强的印刷层次感,因此在印刷的过程中印刷墨色很容易干,因此凹印工艺适用于家居装饰产品,比如适用于实地印刷等等,基于该印刷技术不易产生印刷色差,因此其适合与大宗的印刷产品;丝印工艺顾名思义其印版是丝网结构的,通过刮刀的作用使液体的油墨透过网版图文版面的网孔后,渗透而移印在产品上,从而形成印刷的图文,其最大特点就是印刷墨层厚实,适合于印刷大面积的实地或线条版面的产品,但是,其产品复制的精度不如胶印、凹印或柔印工艺。凹印是印版耐印率最高的一种印刷工艺,其印刷速度也较快,产品复制的精度比较高;数码印刷是计算机技术发展的产物,是当前印刷技术的主要发展趋势,数码印刷能够满足个性化印刷业务的需求,其主要是通过计算机将印刷产品直接印刷到各种制材中,数码印刷技术的应用对于传统印刷技术是一种突破,改变了传统印刷的落后工艺,满足了“互联网+”行动实施的要求。尤其是云技术的发展,带动了“云”印刷技术的发展,可以说大量的个性化印刷需求推动了云印刷技术的应用。与传统印刷方式相比,云印刷能够实现个性化定制、随时下单、快速交货,由于采用网络技术从而优化生产环节,降低了生产成本,可以有效的为客户节省纸张成本。
2印刷技术的发展现状
经过多年的发展我国印刷技术得到创新性的发展,从2006年~2011年全球前12大印刷市场的图表来看,中国已经取代德国和英国成为第三大印刷市场。但是随着技术创新变革的发展,我国印刷技术的发展所取得成绩相比国外先进国家而言还有很大的差距:
2.1我国印刷技术取得的成绩
印刷业在我国的历史发展比较长,因此我国印刷技术相对比较成熟,我国的印刷技术取得了不错的成绩:首先是我国数字印刷技术越来越完善。数字印刷实际上就是通过电脑通过打印装置,直接进行在线印刷的一种新兴印刷工艺,随着数字技术的不断发展和进步,数字印刷已经由简单的彩色打印机,向数字专用印刷机方向发展,印刷材料也由专用的打印纸向包装印刷材料方向转变,印刷幅面由传统的小规格向大幅面方向发展,从而较好地避免了打样与印刷不同工艺之间存在的误差,使包装印刷工艺水平也得到较好的提高。比如现在应用比较广泛的3D印刷技术(见图1);其次印刷设备的性能越来越完善。以半自动化和自动化的设备为例我们在2009年开发出数字压痕机,在接下来的两年中其在国内市场合计销售不超过10台,而2011年销售已超过50台,且之后销售量每年都在以翻番的速度快速提升;最后印刷技术一体化技术应用。DICOweb机上制版商用轮转机特色:无需印版一次影像成像便可不断重复印刷:模块化设计,可以多元化组合:简单更换滚筒套和滚筒.便能印刷一系列不同形式的尺寸和产品.优点:操作概念简单,只须很少人手.综合式的数字印前流程。
图1:3D立体打印
图2:轮转印刷机
2.2我国印刷技术所存在的缺陷
(1)我国印刷技术没有实现绿色化。以凹版印刷为例,凹版印刷占包装印刷主导地位,因其承印材料范围广、印品质量高、高技术含量等特点被广泛应用于食品、药品、烟、酒等行业的包装印刷,并与多项特种工艺相组合而被广泛应用于防伪商标、钞票、邮票等有价证券的印刷,产品与老百姓的生活密不可分,凹印呈现出较强的生命力。但凹版印刷的VOCs的排放严重污染着环境,需要从源头的印刷油墨及胶粘剂水性化、版材的生产制造、印刷生产中的过程控制、凹印设备改造、末端治理中回收装置一体化等方面提出技术问题并积极提出解决方案。
(2)产品性能结构不合理。纵观我国印刷设备的整体现状,目前存在高端设备缺乏、低端设备过剩的问题,这种局面只能会造成印刷行业出现结果不合理的现象,严重影响印刷行业的健康发展。
(3)混合印刷技术应用水平不高。混合印刷技术是未来印刷技术发展的趋势之一,国外先进国家的混合印刷技术已经非常的成熟,但是我国的混合印刷技术还不成熟,尤其是缺乏一个完整的印刷数字生产链。另外我国相关方面的人才也不足,人才不足直接会导致印刷企业发展受到较大的影响。但是当前的高职院校所培养的人才也无法满足此类需要。因此需要国家、高职院校以及企业共同建立共享机制,满足这方面人才的要求。
3我国印刷技术的发展趋势
基于我国互联网技术的快速发展以及印刷包装产业“十三五”发展规划的要求,结合当前国内外印刷技术的发展现状,我国印刷技术的发展趋势主要呈现出以下趋势:
3.1高度自动化
自动化是融合“互联网+”战略的具体体现,随着计算机技术的发展,很多新型的印刷设备已经具备了技术的自动化处理,比如电脑自动技术控制、无轴技术以及光纤传导技术等等。传统的印刷企业车间由于印刷纸张原理材质的问题导致在印刷的时候因为受到环境潮湿的因素而导致印刷工作受到影响,因此印刷厂房除湿机的应用则具有很高的应用价值,实现了对厂房温度的自动控制,当厂房内的湿度以及温度超过预定的温度之后,该设备就会自动停机,同样当实际湿度低于预定的设备之后,该设备就会自动开机,实现了对印刷流程的自动控制。由于该设备的应用大大提高了印刷企业的经济效益和社会效益。
3.2联动化
印刷技术的高端技术带动了印刷设备工作流程的联动化,联动化主要是以模块化、流水化的运行模式进行。尤其是数码技术的发展带动了印刷技术的联动化,实现了印前、印刷、印后各个环节的综合,比如为解决数码印刷后期的连接工作需要,MBOdigital所有规格的印后模块均可以流畅地直接整合到同一个生产流程中,可直接同数码印刷设备连线生产或者连接一个开卷单元离线生产,产品更加符合客户的实际需求,可为客户提供创新高效的完美解决方案。
3.3智能化
智能化是印刷技术发展的主要趋势之一,也是现代数码技术发展的主要象征,智能化是基于互联网技术发展而产生的,其打破了传统的以手工运行为主的模式,实现了无需制版就可以印刷的工作需要。但是我们也要看到我国印刷智能化技术发展的劣势,即食品智能包装有待开发,其结果直接会影响到食品的安全。
3.4绿色环保
坚持绿色发展。绿色环保是“十三五”期间印刷业的工作重点之一。我们要努力达到国家倡导的生产过程的绿色认证标准,在促进印刷业节能降耗,发展绿色环保经济上下功夫。推动低碳循环发展,全面节约和合理利用资源,大力发展废气、废水和印刷固体废弃物的循环综合利用。印刷技术的绿色环保发展趋势主要要做好以下两个方面:一是在印刷设计方面呈现环保理念,很多印刷企业在设计时强化外在的东西,而忽视了环保的理念,结果导致出现过度污染,为此当前的印刷设计体现了环保的理念,在设计创意的时候呈现了以满足客户需求、降低环境污染的特点;二是体现在印刷过程中,我们知道传统的因素过程容易产生各种形式的废液,这些废液对环境的污染是巨大的,因此基于环保任务的要求,绿色技术主要表现在一方面是加大对废液的回收力度,另一方面是提高加强技术创新,积极采取先进的辅料,生产出较为先进的油墨,实现油墨结构的环保化。
结语
随着我国“互联网+”行动的实施,印刷技术通过与互联网技术的结合,促进了印刷技术的快速发展,因此在我国经济结构转型、构建节能型产业的背景下,如何实现印刷技术与现代技术的结合,借助我国现有传统印刷基础条件,实现更合理的数字印刷体系的构建,为企业创造出更大的利益,是我们必须要关注也必须要解决的课题。这就要求每一个从业者贡献自己的精力,致力于更高效、品质更高的印刷技术研发中去,真正让我国成为印刷强国。
参考文献
[1]邓桂芳.聚焦包装印刷技术发展的新趋势和新商机[J].印刷质量与标准化,2014,11期.
[2]薛金萍.苍南软包装行业的发展现状及未来――专访苍南县印刷包装行业协会秘书长陈后强先生[J].今日印刷,2014,06期.
[3]汤兆云.数字印刷技术冲击下胶印版材的发展趋势探[J].东方企业文化,2013,07期.
优化印刷工艺篇3
不同的印刷包装产品工艺流程不同,下面介绍一种常见且具有代表性的工艺盒加工流程,如图1所示。纸张的准备根据客户的要求进行切纸选择色料进行排版印刷覆膜保护及增加光泽根据要求进行UV上光裱纸增加纸张厚度来保证产品质量模切粘合组装。粘合组装可以根据待加工纸张的数量来选择何种方式进行作业,如果数量多和交货期短,便可选择加工速度快的糊盒机进行加工。
2印刷包装生产线模型
2.1模型的定义及边界的确定(1)根据印刷包装生产制造过程的特点以及在制品缓冲区的现状,在保证逻辑结构的基础上,建立了印刷包装生产线的印刷包装的总工序,如图2所示。待切纸张储存在缓冲区B中,而后进入切纸区E1,切好的纸张经过缓冲区B1进入印刷区E2。为了实时监测纸张的印刷效果,需要阶段性抽查纸张的质量,以观察印刷的色调,及时动态地调整相应的色彩。本工序以一个分流模块F来设定抽查纸张的概率,B3为未被抽查到的纸张缓冲储存区,B2为抽查到的纸张缓冲储存区,经C1判定模块判断纸张的质量;合格的纸张送至缓冲区B3进入下一步工艺,不合格的则进入缓冲区B9回收处理。印刷合格的纸张进行覆膜工艺E3,经判定模块C2将覆膜合格的纸张送入缓冲区B4进行下一步生产工艺,不合格的送入缓冲区B9。(2)由图2可知,生产线工序的加工设备E={E1,E2,E3,E4,E5,E6,E7};缓冲区B={B1,B2,B3,B4,B5,B6,B7,B8,B9}。粘合组装存在人工组装和机器糊合两种加工工艺,不同的加工工艺生产周期不同,效率也有所区别。影响生产单元系统结构和在制品缓冲区动态变化过程的因素较多,建模时提出以下假设:生产设备完全可靠、无故障;缓冲区B有充足的货源,除了印刷E2和覆膜E3加工设备有检测纸张质量外,其他设备生产的产品均认为合格;忽略印刷机的校板时间;各在制品缓冲区的容量有限。
2.2基于TPN的建模Petri网由CarlA.Petri博士提出,它是一种可视化图形,描述离散事件系统的静态结构和动态特性。本文采用TimedPetriNet(TPN)的建模方法,通过包含时间参数的库所和变迁,描述事件驱动离散系统(DES),有效地对具有并发、同步和冲突等动态过程进行模拟和分析[6]。TimedPetriNet定义为如下六元组[7-8]:TPN={P,T,I,O,M,D}其中:库所(Place)的有限集合采用P={P1,P2,•••,Pn}表示,n0为库所数量;变迁(Transition)有限集合采用T={t1,t2,•••,tm}表示,变迁数量为m0;P∩T=Ф;输入函数为I:PXTN,定义了从库所P到变迁T的有向弧的重复数或权的集合,N={0,1,•••}为非负整数集;输出函数为O:TXPN,定义了从变迁T到库所P的有向弧的重复数或权的集合;PN的标识为M:PN,它是一个列向量,Mi表示第i个库所中的令牌(Token)数目。每个令牌赋有其隐含特征属性和库所的时间信息,为一维行向量TK={d1,•••,dn}(1Xn),n0为库所的数量,di表示第i个库所的延时。D:TR+(正实数域),表示库所的延时集合,它为一个kXn的矩阵,其中k0为令牌的数量,n0为库所的数量。印刷包装生产线是由多个加工单元组合而成,因此,根据模型图2分析生产单元的布局特点,首先对在制品缓冲区进行分类,并建立相应的Petri网模块,包括:①在制品从一台设备经在制品缓冲区流向下一台设备(如P1P2P3);②在制品从一台设备经具有分类作用的缓冲区分别流向多个缓冲区(如P7P8P9/P19)。其次将各加工设备和缓冲区之间的关系描述成Petri网中的库所、变迁及其相应的活动,定义各模块之间连接所需的变迁或库所,建立印刷包装生产线总TPN模型,如图3所示,模型说明如表1所示。通过TPN模型,描述了印刷包装生产过程的离散的制造过程,为下一步图形化的仿真模型的建立奠定基础。在TPN的有向图中,库所采用圆圈表示,变迁采用矩形表示,令牌采用圆点表示,带有令牌的库所表示在制品存在设备或缓冲区中。部分库所因有容量的限制而形成抑制弧,用k表示,k(Pi)=mi。文中采用的变迁ti表示经一定时间后发生的事件或操作,将时间与变迁关联(赋时变迁),一旦变迁使能,则立即从该变迁的输入库所中移去一定数量的令牌(完成在制品的运送),但变迁要延迟一段时间(满足加工时间或缓冲时间的要求)后再触发,并在输出库所中放入一定数量的令牌。然而,并不是每个变迁都是赋时,有些变迁的延时相对非常小,可以忽略不计;有些变迁(如Ti)表示控制逻辑,本身无延时[9]。
3印刷包装生产线的仿真
对于复杂系统,系统的解析式难于描述和求解困难等问题,而仿真是一种有效解决复杂系统的研究方法。虽然TPN模型可以描述一个离散事件系统的动态行为特征,但是,印刷包装制造过程的运行、调度和控制是现场工程技术人员的工作,这样的TPN模型对于工程技术人员来说比较抽象,研究人员需要为工程技术人员提供一个易于理解和操作的工具。因此,运用仿真平台eM-Plant将Petri网模型中的库所和变迁进行映射,使其与仿真模型中的实体相对应,并设置实体的相关参数,即可形成直观的生产系统的仿真模型,从而实现从Petri网模型到eM-Plant模型的转化。
3.1eM-Plant在生产制造领域应用较广的仿真软件eM-Plant,由以色列Tecnomatix公司开发,主要用于生产系统与生产过程的建模与仿真的软件系统。用户可在eM-Plant环境下分析和优化生产系统的各种性能指标如生产率、在制品水平、设备利用率和工人负荷平衡等。
3.2仿真模型的框架在印刷包装过程的TPN模型的逻辑结构基础上,运用eM-Plant仿真软件将图3所建立的TPN模型进行映射,具体过程如下。(1)设置对象及模型映射eM-Plant将系统的基本对象划分为四大类:物流对象、信息流对象、服务对象以及移动对象(MU),并按照生产工序进行连接。基于表1的定义,仿真模型的参数映射说明如下:库所P0映射模型中的待切纸缓冲区B;P1,P3,P7,P10,P12,P14和P16分别映射为加工设备E1,E2,E3,E4,E5,E6和E7,P18,P20映射仓库Drain1和回收站Drain2;模型中的普通缓冲区B1,B5,B6,B7和B8是由库所P2,P11,P13,P15和P17映射而来,分类缓冲区B3,B2,B4,B9则由P4,P5,P9,P19映射所得;库所P6,P8分别映射为判定模块C1和C2。(2)定义对象及变迁触发在仿真模型中,Source对象更名为Entry,表示纸张原料的投入(加工单元入口),并在MU属性里选择MUs中的纸张paper对象,用来描述系统中的物流;SingleProc对象表示各加工工艺或判定模块,即触发变迁t1,t3,t5,t7,t9,t11,t13,t4,t6进行工作;缓冲Buffer对象表示纸张由一个工艺转移到下一个工艺的过程;如果Ei的纸张paper移动到Bi上,表明纸张paper在该工艺加工完成或判定结束准备进入缓冲区,即触发变迁t2,t8,t10,t12,t14;分流对象FlowControl将纸张paper送入相应的加工单元中;对象Drain表示工件加工结束(加工单元出口),储存或回收不合格产品,即触发变迁t15,t16;对象Chart用来显示加工设备的工作情况;TimeSequence实时记录产品;对象Gauge监控缓冲区B中纸张的数量;两个变量Variable(Counter1和Counter2)计算经过印刷和覆膜加工设备的数量MU来设置检测工作模式,使产品分类处理;对象Method为SimTalk程序控件,在事件发生时触发该程序,从而实现对该事件发生的控制。由此建立的生产线的仿真模型如图4所示。
3.3离散事件及其控制通过对印刷包装生产线的系统进行仿真,可以建立应用对象模型,对系统各离散事件的组织行为和交互作用进行分析。eM-Plant的每个对象都包括属性和事件,属性是对象的特性,而事件则是指对象的状态发生变化。在本次建立的仿真模型中,通过时间和事件触发两种方式来调用对象SimTalk语句,从而控制仿真模型的运行和状态的变化。仿真具有对仿真模型的事件控制和算法控制。印刷包装生产系统中的事件控制是通过对对象EventControl的操作来实现,并在模型中加入两个对象Reset和INIT进行模型的重置和初始化。算法控制通过控件Method来实现。系统的主要离散事件在于印刷和覆膜工序中对加工后的产品进行验证,即要求在模型中对印刷和覆膜两个加工设备工作概况给予调整,其Method控制流程图如图5所示。图5印刷和覆膜程序控制流程图印刷后的产品,采用分流对象FlowControl设置抽查纸张paper的比例。编写程序前,在纸张paper的属性CustomAttributes中设置一个名为quality的属性,令其Value值为Good,数据类型Datatype为字符串string。根据2.1节中的工序,采用SimTalk语言,撰写程序并封装在Method对象Work1(2)和Move1(2)中,使其分别在B2(E3)和C1(C2)的控制属性Exit被调用。对象Work1(2)的作用是判断印刷和覆膜后纸张paper的质量,然后通过对Move1(2)中程序的调用,使不同质量的纸张paper选择正确的路径,贯彻下一步加工工艺。在每个加工设备的作业中,需要准确描述活动的执行时间,如纸张paper的加工时间以及缓冲(搬运)时间,另外,还要设置缓冲的容量限制,即k(Pi),所有这些参数都可通过对SingleProc对象的属性进行修改。为了便于对仿真数据分析,在TimeSequence的Record处设置Value值为Drain1.numIN,系统记录了合格工件加工完成的时间和数量。
4仿真结果的分析及生产过程的优化
4.1仿真数据和瓶颈分析以某印刷包装企业的月饼礼盒包装的生产流程为仿真对象,生产过程如下。该产品的客户生产要求为:275克镭射银卡纸四色印刷覆膜(光膜)UV工艺裱纸(300克白板底纸)模切成型粘合组装质检入库。由于订单数量为20000个,统计生产线各机器的历史作业时间和分析生产成本,粘合组装工艺采取人工组装的方式。通过调研车间各设备的加工速度和作业时间,在仿真模型中输入加工参数:切纸机E1:0.5秒/张;印刷机E2:0.5秒/张;覆膜机E3:2秒/张;UV丝印机E4:2秒/张;裱纸机E5:8秒/张;模切机E6:5秒/张;粘合组装E7:10秒/张;输纸Entry:共计20000张;缓冲装置容量与缓冲时间如表2所示。(1)图表数据。eM-Plant的分析工具—统计分析、图、表,可以分析缓存区和设备的利用率。因此,通过创建统计数据和图表,对生产线工作负荷和设备生产效率等生产性能参数进行动态分析,并比较生产线现行的状况与理想状况的差距,找出瓶颈资源进行优化[11-12]。根据模型的仿真,得出1~7小时的仿真数据统计,如表3所示。(2)瓶颈分析。根据约束理论和仿真数据来分析生产瓶颈。约束理论(TheoryofConstraints,TOC)指出,系统的生产效率是由系统中一个或者几个约束环节(瓶颈)所决定。而生产系统中常见的瓶颈资源通常为某工作中心或某台生产设备,其使用率最高、生产负荷超过生产能力。因此,通过对生产设备不同时刻的仿真数据,可得出该生产系统的使用率较高且持续上升的加工设备,由表3数据可知裱纸机和粘合组装工序为瓶颈工序。然而,生产中存在不确定的因素,易造成生产瓶颈的变动。TOC的关键就在于不断突破系统约束,合理调节瓶颈设备以增加系统生产效率,并针对性地对系统瓶颈资源进行改进[13]。文献[14]对瓶颈转移的成因进行了深入分析,提出了相应的预防与应对方案。因此,为了保证在规定加工时间内正确识别瓶颈资源,需对每台生产设备在相应时间段内的工作负荷率进行分析。当系统继续仿真至11小时后,其工作状况如图6所示。由此可知,从1~11小时的仿真,裱纸加工E5和粘合组装E7的任务负荷率最大,根据TOC的基本思想可判断E5和E7为该生产系统的瓶颈设备。
4.2生产过程的优化生产过程的优化是指合适地选择离散变量,使系统的某一性能指标实现近优或最优,最大限度地利用和合理分配资源,为企业降低生产成本和提高生产效率[15]。因此,可将生产线作为一个整体进行优化,通过合理配置各生产设备的节拍以及员工数,最终提高生产效率。此外,缓冲区容量的大小也直接影响生产效率。因此,在系统缓冲区容量总和一定的条件下,优化配置生产线各缓冲区的容量是提高系统性能指标的有效措施之一[16]。对于具有瓶颈设备生产系统,可以采用一定的加工工艺减少瓶颈工序的加工时间[17]。而在印刷包装企业中,为使其能够发挥自身生产能力制定出合理的生产计划,满足客户的需求,文献[18]以约束理论及生产排程为指导思想,进行瓶颈资源的识别,给出了基于约束理论思想的详细解决方案,实现资源共享与优势互补。综上考虑,根据生产系统存在的问题,设置模型中设备的相关参数,进行仿真实验,提出生产线的优化方案如下:(1)减少切纸和印刷加工区的操作人员数量,降低工位的生产周期、增加操作时间。(2)平衡系统中各工位的生产节拍和缓冲区容量的大小,提高设备的利用率,防止出现太多的空闲或加工繁忙的状况。根据上述优化方案要求可以将切纸机E1、印刷机E2的加工速度调整为1秒/张,并增加E3,E4,E5,E6,E75个工位的操作人员的数量来缩短该工位的操作时间,将覆膜机E3,UV丝印机E4、裱纸机E5、模切机E6、粘合组装E7的加工速度分别调整为:1.5秒/张、1秒/张、2秒/张、2秒/张、5秒/张;缓冲区容量与缓冲时间调度如表4所示。通过上述仿真参数的优化,运行仿真时间为7小时,观察系统的生产情况,如图7所示,可以发现,瓶颈设备E5和E7在运行6小时后,设备占有率开始下降。通过TimeSequence对象记录的数据,如表5所示,优化方案生产出的首件产品时间虽然比原方案长,但随后的生产速度为原方案的两倍,达到5秒/张。这说明新方案充分利用了生产资源,为企业的生产管理和优化调度提供了决策支撑。然而,实际生产中要综合考虑诸多因素的影响,比如动态的离散生产系统随着加工时间的延长,控制变量随离散状态而变化,瓶颈设备可能会发生漂移,导致上述给出的优化方案不一定适用。因此,根据不同生产环境的特点,不断调整各加工设备的速率和在制品缓冲容量及时间,并通过多次仿真实验,反复优化,实现近优或最优方案。
5结论
优化印刷工艺篇4
关键词:陶瓷装饰;高清三维胶辊印刷;凹凸釉面砖;喷墨打印;优势
1前言
釉面砖由于具有多色彩、多变化和更好的表面装饰效果等优势,已成为厨房、卫生间、阳台等空间装饰的主要选择。釉面砖的传统印刷生产技术主要有丝网印刷、辊筒印刷、胶辊印刷等,由于胶辊印刷的产品图案纹理清晰、连贯自然、仿石效果逼真,已经成为陶瓷砖主流印刷生产技术。但传统的釉面砖生产技术都只局限于平面印刷,新研发的喷墨打印技术,是一种非接触性的印刷模式,可在凹凸面上喷墨印刷,具有生产技术数字化,转换生产灵活简单,易于实现个性化等优点,把陶瓷釉面砖的艺术表现力与空间层次美感大大地推进了一步,但也存在以下不足:
(1)喷墨的核心设备喷头及墨水还要依赖进口;
(2)墨水的颜色单一,缺乏深红色;
(3)打印速度慢,生产效率低、成本高;
(4)喷墨打印设备的购置和维护费用相当高:
(5)其核心知识产权为发达国家所掌握。
为了突破传统印刷技术和喷墨打印技术的不足,笔者通过大胆技术创新,首创了高清三维胶辊印刷技术,突破了在瓷砖上实现立体高清、高速印刷的世界性难题,并开发出具有能工巧匠精雕细琢后的天然石材独有韵味的高清三维凹凸釉面砖产品。从而满足了人们对高品味和个性化生活环境的追求,已成为釉面砖产品中的新宠。
2试验内容
2.1印刷胶辊的结构分析和设计
对于普通的辊筒平面印刷,一般采用中等硬度的材料(SD橡胶)制作印刷胶辊,但如果采用这种材料制作的胶辊在凹凸表面印刷时,就会出现缺花现象(花纹在凹凸连接处不连续),如图1所示。
为了实现高清三维胶辊印刷技术,笔者通过建立胶辊的有限元模型,从理论上探讨结构改进的路径和方法。当胶辊与砖坯接触时,胶辊和砖坯之间的移动导致受力变形。一般的凹凸胶辊印花可分为三阶段。第一阶段:胶辊进入凹槽的一个侧面接触,侧面与胶辊的运动方向相厂,胶辊与侧面相互离开,变形主要是由于胶辊自上而下的正压力导致:第二阶段:胶辊咬入凹槽内。主要特征是胶辊与凹槽底面接触,凹槽宽度和胶辊变形程度不同,如果充分变形并填充,会呈现三个面和两个面同时接触的情况:第三阶段:胶辊离开凹槽。胶辊与凹槽第二个侧面接触,胶辊与侧面相互的挤压除胶辊向下的垂直压力外,还有相对运动产生的水平压力。其中,最复杂的孤岛型凹槽(凸起)印花,凹凸的四个侧面都需要很好地贴合。为了观察贴合效果,简化计算复杂度,在建立胶辊有限元模型时做了一些必要的假设和近似,如图2所示。取胶辊局部进行分析,分为橡胶层和钢筒层,胶辊弹性模量取8MPa,泊松比为0.45。钢筒采用A3钢材料参数。在胶辊表面取一定面积给定位移约束,考察胶辊变形和受力情况。其计算结果如图3、图4所示。
通过分析发现,在这种结构下胶辊要达到规定位移量。其底部的应力应达到11.7MPa。随着位移量增加,最大应力值将迅速增加。在实际应用中,硬胶辊缺花是因为原有的胶辊支撑结构提供的胶辊压力偏小,不能使胶辊产生足够的变形。但如果加大压力,会破坏砖坯的表面。因此,考虑以软胶代替硬胶,使其在较小胶辊压力下可以产生足够的变形,就可以解决这些问题。
软胶辊的有限元模型中,使胶辊弹性模量变为2MPa,其分析结果如图5、图6所示。
由图5、图6分析可知,改变材料参数后,同样的变形量,其最大应力约为2MPa。即在同样压力下。软质材料能更好地贴近凹凸面。但从变形效果上看,软质材料和硬质材料胶辊的变形效果接近,变形的斜面倾角度在600-630之间。当凹凸面倾角度超过此范围,胶辊与凹凸侧面就不能较好地贴合。
为了增大变形斜面倾角,研究采用软硬组合胶辊结构。建立了如图7所示的双层胶辊有限元模型。采用同样的加载方式,得到的变形效果和应力分布如图8所示。
由图8分析可知,在相同变形情况下,其最大应力约为3.25MPa,而变形侧面倾角变大为65°-680°结果表明:双层胶辊结构与软质胶辊相比其压力略有增加,但变形倾角明显加大,有利于胶辊与凹凸侧面的贴合。
基于以上理论分析,选择了软硬双层胶辊结构的同时,对胶辊支撑系统也做了相应调整。进一步研究发现,双层胶辊厚度比、凹凸高度差、胶辊外径等参数与软硬胶辊的体积比相关。在相同厚度比的情况下,凹凸高度差越大,软胶体积比越大,有利于改善胶辊应力分布。当凹凸高度差超过软胶厚度时,体积比与胶辊直径和凹凸高度的关系如图9所示,胶辊直径与体积比关系如图10所示。
由图9、图10可知,当胶辊直径越小,在相同变形情况下,软硬胶的体积比增大。因此在满足其它工艺条件的基础上可尽量减小胶辊直径。
由于理论分析模型对胶辊做了适当的简化,同时在试验的基础上进一步对胶辊结构进行了优化。优化和改良后的印刷胶辊,不仅适应凹凸表面高度差达到6mm的釉面砖,而且在凹凸变化面上都能保证纹路的清晰和连续。
2.2印花釉的试制
为了达到高清三维凹凸釉面砖的印花效果。笔者将市场上现用的各种印油、基础釉粉、色料按一定比例混合球磨,用所确定的高清三维软硬双层专用胶辊分别在凹凸位高度达6mm的砖面上进行印花,发现现有的印油由于聚合力、性不好,不能够在凹凸不平的砖面上印刷出完整清晰的图案。
通过分析,发现高清三维凹凸釉面砖由于凹凸位高度差较大、胶辊的材质软,辊筒与砖面的摩擦力大、印刷的图案网点在不受外力的作用下会变形。且胶辊上的网孔因外力的挤压会变形,这一系列原因造成花釉难于填充。要克服这些缺陷,要求花釉必须要有较高的聚合力和弹性,以确保在外力作用下不变形不软蹋。同时,花釉还要具有较好的性、较强的渗透力,以确保花釉能够填充到胶辊因受外力作用而变形的网孔内。并在与釉坯接触瞬间,将网孔内的花釉印在砖面上而形成清晰完整的图案。从花釉的构成来看,它是由釉粉、色料、印油组成,因此,印油的性能非常关键。
通过笔者多次试验,结合现有印油的性能,采用复合有机材料代替了传统单一的有机材料,试制出适合高清三维凹凸釉面砖生产所需的专用印油,并按一定比例与釉粉、色料调配出性能好、聚合力强的印花釉。高清三维凹凸釉面砖生产专用印油的配方组成、不同印油的工艺参数、不同花釉配比见表1~表3,不同花釉的印花效果见图11~图16。
从表3可以看出,在所有条件不变的情况下,只改变基础釉粉的含量,其花釉比重随基础釉粉的量降低而降
低,其流速也发生一定的改变。再由图11-图16中可以看出。1号花釉印花效果很差,凹位完全没有图案,纹理不清,且有大量白点;2号花釉印花效果不理想,凹位可见少量图案,但纹理不清晰,有大量白点;3号花釉印花效果不太理想,凹凸位连接处图案不连续,纹理图案模糊,且有白点:4号花釉印花效果较好,凹凸位高度差小的产品凹凸位连接处图案连续,纹理清晰,但凹凸位高度差大的产品凹位印不到花;5号花釉印花效果较好,凹凸位高度差小的产品凹凸位连接处图案连续,纹理清晰,但凹凸位高度差大的产品凹位图案模糊且有白点;6号花釉印花效果好,凹凸位高度差达6mm的砖面上图案清晰,凹凸位连接处图案连续不间断,仿石效果逼真,完全达到高清三维凹凸釉面砖所预定的效果。
2.3成形工艺及模具的研究
由于凹凸釉面砖坯表面设计成凹凸图案(砖面凹凸位高度差达到6mm),若采用传统的表面朝下,背面朝上的反打成形工艺,会造成脱模困难。压制好的产品在推出模具时易将凸位的边角位推变形,甚至产生破损,影响冲压质量,并且产品在压机运输平台的辊棒上运行时,会因凹凸不平而产生震动,从而造成裂坯、烂坯等问题。同时,模具的磨损快,且冲压速度不能快,制约了生产。为了保证产品的凹凸效果及提高冲压成品率,笔者通过反复试验,突破传统反打工艺,采用了砖表面朝上的正打成形工艺。
由于本技术研制的高清三维凹凸釉面砖,其表面有凹凸,成形工艺设定为“正打”工艺,这样必须对成形模具进行改进。模框不改变,正打的砖坯出模时会出现正面大,底面小的情形。坯体在出模时,一方面其正面边角在模框侧板作用下容易被崩烂,影响坯体成形效率;另一方面产品正面的倒角容易在坯体上模边形成倒钩形,倒角越大,倒钩也越大。倒钩一方面影响砖坯脱模;另一方面影响排气。通过实验,对产品正面的倒角进行了优化,将“正打”产品的倒角设计为R5,将倒钩减到最小,保证了气体的排出,使凹凸砖坯密度均匀,且有较高的成形效率。
2.4粉料粒度及模具压胶硬度的优化
半干压成形的粉料具有一定的颗粒级配,由于布料器来回运动产生振动,会使较细的粉料通过大颗粒的间隙向下运动。因此砖坯的下表面光滑平整,这也是一般半干压成形采用反打的原因之一。但凹凸釉面砖采用正打工艺,试验发现成形的坯体经素烧后,砖面有明显的大颗粒,特别粗糙。淋釉后,釉面不平,有皱纹釉、桔釉等缺陷。因此笔者通过对喷雾塔喷片、旋流片及柱塞泵压力进行调整,从而对粉料的颗粒级配进行了优化,并将成形模具的压胶硬度提高,进而保证了素烧后砖坯表面的光滑。
3结果分析与比较
采用上述高清三维胶辊印刷技术生产的凹凸釉面砖产品,图案清晰,凹凸位连接处石材天然纹理连贯自然、颜色丰富,该产品具有能工巧匠、精雕细琢天然石材独有的韵味,增强浮雕的表现力,极大地丰富了釉面砖的装饰效果。经检测,产品各项指标与正常生产的釉面砖一样,完全符合GBfr4100-2006附录L、GB6566-2011中A类装修材料和HJ/T297-2006标准要求。高清三维胶辊印刷技术通过对普通胶辊印刷技术的研究,解决了胶辊印刷技术无法在凹凸釉面砖上进行高清三维印花装饰的重大技术难题。实现了通过在凹凸釉面砖表面进行一次性印刷装饰,就可达到目前国外最新喷墨打印技术所具有的高清三维印刷效果。为了进一步分析该技术的优越性,笔者将目前市场上的各种装饰技术在生产效率、适应性、图案分辨率、性价比方面进行了比较,其结果见表4~表6。
从表6可知,高清三维胶辊印刷技术具有更高的性价比和更适合大规模生产的经济性。
4结论
(1)高清三维胶辊印刷技术突破了建筑陶瓷行业广泛应用的胶辊印刷技术不能在凹凸釉面砖表面进行快速高清印刷装饰的难题,打破了国外对瓷砖立体印刷技术的垄断。
(2)本技术在表面凹凸有釉陶瓷砖胶辊印刷技术领域,综合技术经济指标和产业化规模,与国内外同类技术相比,具有明显的优越性。
(3)高清三维胶辊印刷技术的成功,提升了我国建筑陶瓷砖的生产技术水平和装饰技术水平,促进了建筑陶瓷产品市场的多元化发展,社会效益显著。
优化印刷工艺篇5
烟包凹印特点
我国烟包的印刷需求主要体现在两个方面:其一,我国烟包设计以实地色块为主,且大部分烟包的主题图像以抽象图案为主,网目调图像运用相对较少,因此,在烟包印刷过程中,要求烟包实地部分色相稳定,色彩饱和度高;其二,我国烟草行业重组和卷烟品牌整合的工作已基本完成,单个卷烟品牌的规模较大,因此要求烟包印刷具备生产效率高、生产成本低的特点,而这些需求恰恰是凹印的优势所在,这也是凹印在烟包印刷领域得到广泛应用的主要原因。
1.色相稳定,色彩饱和度高
凹印产品的色相和饱和度是由凹版的网穴深度及凹印油墨的黏度来决定的。由于凹版表面镀铬层的硬度很高,因此凹版的网穴深度在实际印刷过程中是基本不变的,而凹印油墨的黏度则需操作人员进行定期检测或利用凹印油墨自动黏度控制系统进行控制,以达到良好的油墨黏度控制效果,使凹印能轻松满足烟包印刷对色相稳定性的要求。同时,凹印的墨层厚度较大,因此凹印产品的色彩饱和度也相对较高。
2.生产效率高,生产成本低
目前,国产凹印设备的印刷速度基本可达200米/分钟以上,相当于先进胶印设备印刷速度的2倍左右。另外,凹印设备能够实现卷筒纸连续印刷,以及联机压凹凸、模切等高效自动化生产,相比其他印刷方式,具有生产效率更高、生产成本更低、更适合烟包大批量印刷生产的优势。
烟包凹印新技术
围绕“规模化、低成本、高效率”的主题,国内烟包印刷企业进行了大量的技术研发工作,并取得了显著成果。在此,笔者将重点介绍烟包凹印中的卷筒纸分段凹印和多工艺集成凹印两种新技术。
1.卷筒纸分段凹印技术
卷筒纸分段凹印技术的工艺流程为:凹印全息定位烫印模切(带压凹凸)成品。
(1)卷筒纸凹印过程采用无缝拼接方式进行雕版拼接,每张纸可减少10mm左右的叼口耗用量,相当于节省了近2%的纸张耗用成本,因此卷筒纸凹印技术特别适用于大规模烟包印刷,可使烟包印刷企业获得可观的经济效益。
(2)卷筒纸定位烫印技术的主要优势在于:①生产效率高,单张纸全息定位烫印的速度一般为5500张/小时,而卷筒纸全息定位烫印的速度一般为80米/分钟(约9795张/小时);②套印精度高,一些业内人士担心卷筒纸定位烫印如此快的速度会对套印精度造成影响,而实际上,由于卷筒纸定位烫印技术使用的是电机模拟跳步技术,其套印精度反而比单张纸定位烫印的套印精度更高。一般,单张纸定位烫印的套印误差为±0.10mm,而卷筒纸定位烫印的套印误差为±0.05mm,且产品烫印合格率基本保持在99%以上;③烫印效果好,卷筒纸定位烫印的实现过程为线接触,烫印箔内的空气可被完全排尽,烫印产品表面光亮,因此卷筒纸定位烫印技术拥有单张纸定位烫印技术所无法超越的防伪功能。
(3)卷筒纸模切过程可同时完成压凹凸和模切两道工序,这样不但能提高烟包质量,还可提高烟包印刷的生产效率。
2.多工艺集成凹印技术
对于集多种工艺于一身的薄型烟包印刷,因薄型纸需要在多种工序之间流转,伸缩变化较大,因此难以满足各个工序的生产工艺条件,特别是对套印精度要求很高的胶印、网印和压纹工艺,往往容易导致烟包印刷生产效率低、合格率低、产品质量差。为解决上述问题,专注于烟包凹印技术的研发人员通过多次试验,攻破了以下三大技术难关,最终实现了多工艺集成凹印技术。
(1)解决了普通镭射纸的版缝问题和卷筒纸凹印套印问题,实现了无版缝镭射纸的卷筒纸凹印生产。
普通镭射纸存在人眼可识别的明显版缝,一般版缝宽度为1~3mm,若应用于卷筒纸凹印生产工艺,将会因版缝问题产生大量废品,而无版缝素面镭射纸则可大大提高产品的合格率。同时,由于普通镭射纸反光度极高,当将套印光标直接印刷在其表面时,容易导致套准识别系统报错,影响套印精度。对此,研发人员设计了一种专用纸张,解决了普通镭射纸在进行卷筒纸凹印生产难以套准的缺陷。
(2)通过优化压凹凸辊工艺参数及应用压凹凸辊防错位和过压保护技术,实现了凹印与压凹凸工艺的集成生产技术。
目前,常规的凹印联机压凹凸工艺基本上都是在厚卡纸上实现的,而薄型纸在凹印联机压凹凸过程中容易因公母版错位而形成剪刀口,从而导致烟包爆口现象,大大增加废品率。对此,研发人员通过对联机压凹凸辊进行重新设计,使薄型纸凹印联机压凹凸工艺得到了规模化生产应用。
(3)通过优化凹版工艺参数、提升凹印油墨性能,实现了凹印与胶印、网印工艺的集成生产技术。
通过调整凹版的雕刻参数及凹印油墨的性能,采用激光雕刻工艺实现深网穴凹印,以及在层次还原上设定多层次雕刻参数,采用凹印专用光变防伪油墨同样达到了胶印层次感强及网印墨层厚实的效果。
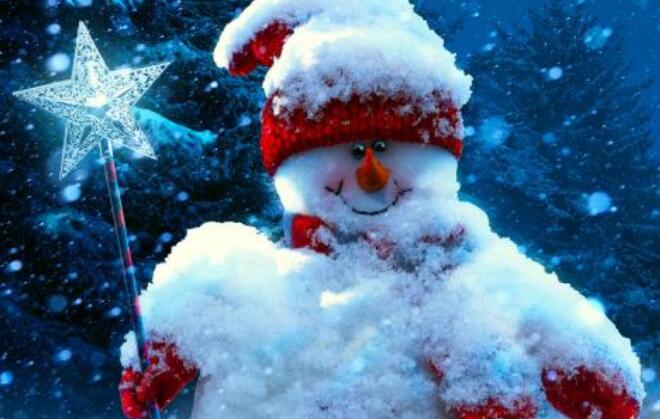
美丽校园的演讲稿范文(整理8篇)
- 阅0美丽校园的演讲稿篇1尊敬的各位老师,亲爱的同学们:大家上午好!今天我国旗下讲话的主题是”把美丽带进校园“。走在校园里,看见地上的一片纸屑,你是视而不见,还是弯腰捡起?在食堂.....
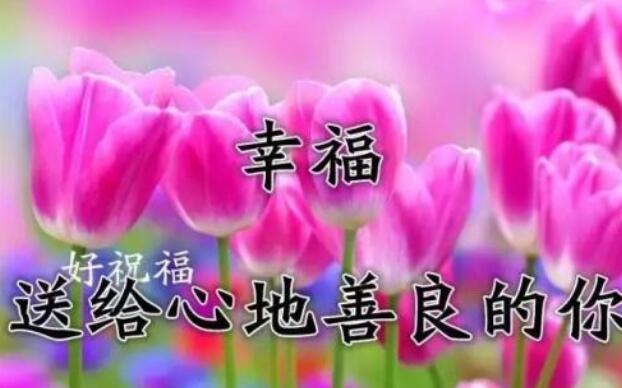
植树节的作文范文(整理16篇)
- 阅0植树节的作文范文篇1今天是植树节,阳光灿烂,老师安排我们一起去植树,我们开开心心地拿起水桶,抗起铁铲,带上树苗地去植树了。我们兴高采烈地来到路边,我和小明一组,我挖坑,小明提水.....
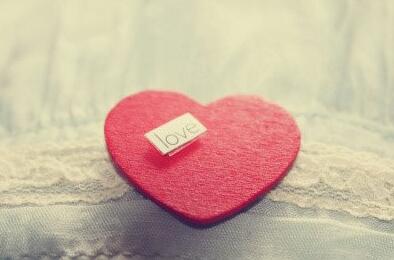
高三周记范文(整理5篇)
- 阅0高三周记范文篇1缘和馨是很要好的室友,她们无话不说,常常听到她俩在一起唱:“记忆是阵阵花香,一起走过永远不能忘。”缘有一件很漂亮的白衣裙,那是她母亲送给她的生日礼物,她把白.....
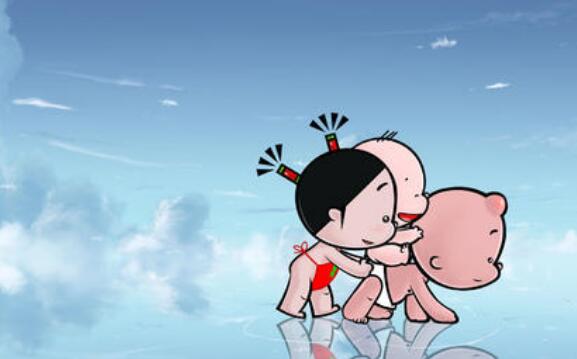
关于寒假周记初一范文(整理2篇)
- 阅0关于寒假周记初一范文光阴似箭,日月如梭,一眼间,我初一年的寒假生活已经接近尾声。让我来回味一下这个寒假令我难忘的事。寒假中我们迎来了中国最传统的节日——春节。除夕那.....